Next-Level Distillation
Aquaback's technology sets new standards for energy efficiency and cost-effectiveness
Aquaback’s distillation-based technology achieves the gold standard of water purity but provides more efficient, cost-effective, and environmentally friendly solutions.
85%
More Energy Efficient
70%
Lower Capital Cost
80%
Ammonia Removal
100%
Calcium Carbonate Scaling Elimination
While distillation guarantees pure water, its high energy requirements, expensive equipment, issues with calcium carbonate build-up, and limited effectiveness in removing ammonia have hindered its practical scalability for various solutions.
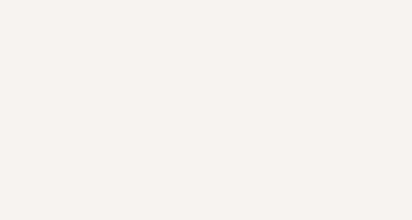
Aquaback utilizes state-of-the-art thermodynamic principles and advanced vapor compression techniques to achieve highly efficient and sustainable water purification.
Improve energy consumption.
Aquaback distillers use less than 20 Watt hours per gallon of distillate by recycling approximately 99.3% of the heat of vaporization. This represents a 85% improvement vs competing vapor compression distillation and an over 99% improvement over traditional distillation.
Decrease capital costs.
Our patented distiller design operates at lower pressures, allowing for lightweight, welded sheet metal construction. This reduces the weight and cost of materials, estimated to reduce manufactured cost by over 70% more affordable.
Achieve superior ammonia removal.
Aquaback's patented process effectively removes almost all the total nitrogen by removing approximately 80% of nitrogen as ammonia and 100% as nitrate.
Eliminate calcium carbonate scaling.
Aquaback's mechanical process prevents the accumulation of CaCO3 scaling on the evaporator surface, eliminating the need for frequent and costly maintenance associated with scaling issues.
Monitor conductivity.
Aquaback distillate purity allows effective conductivity monitoring of purity, bypassing the need to monitor individual contaminants, assuring optimal performance and consistent water safety.
How it Works
Thin Film Application
A very thin film (1/100th inch) of dirty water is mechanically applied to the surface of the evaporator.
Steam Generation
Within 1.5 seconds, the top half of the applied film transforms into steam.
Compression
The steam is compressed at a low pressure of 0.8 psi.
Condensation
The compressed steam is directed to the condenser, which is located on the backside of the evaporator and separated by a thin heat-conductive sheet metal (typically CuNi). The steam condenses at approximately 214.5 F, releasing heat.
Heat Transfer
The released heat travels through the sheet metal to drive evaporation.
The above heat balance is for a 20 g/hr distiller processing 22 g/hr of dirty water
Cleaning to Prevent Scaling:
Every 1.5 seconds, the evaporator surface is wiped almost clean, removing any residue from the previous cycle, and a new thin film of dirty water is applied. The regular cleaning and reapplication process prevents the formation of CaCO3 scaling on the evaporator.
Efficient Heat Management:
The system recycles approximately 99.3% of the heat of vaporization. During startup, latent heat is introduced as the distiller is heated to nearly 212F. About 5/6 of the heat circulates between the evaporator and condenser, remaining within the system. Around 1/6 of the heat attempts to leave the closed system. This occurs through the distillate and concentrate streams, venting gas, and imperfect insulation.
The majority of the heat loss is minimized through a proprietary counterflow heat exchanger, which operates with approximately 97% efficiency. This results in less than 1% loss of the heat of vaporization. The lost heat energy is replaced by new sensible energy provided by the compressor.
No additional energy is required for the process, as the heat energy is efficiently recycled within the system.
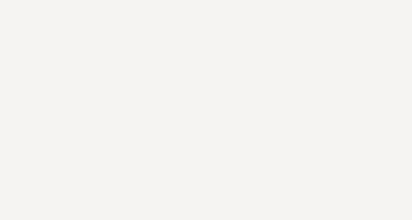
Explore the possible applications for Aquaback’s efficient, cost-effective, and environmentally friendly solutions.
Centralized Treatment Plants
Aquaback's innovative technology offers water treatment plants a reliable, efficient, and long-term solution.
Potable Water Solutions
Advanced treatment solutions for improving water quality for both everyday use and for emergency situations, military operations or underserved villages lacking access to treated water
Wastewater Recycling
Enhance water availability, improve water quality, and overcome the limitations of centralized water paradigm.
Industrial Wastewater
Compact and Sustainable solutions to create completely clean water
Septic
Septic retrofits and new septic installations that eliminate all pathogens, reduce nitrogen to very low amounts, and require a small installation footprint.
Green Hydrogen
Aquaback plays a vital role in supporting the production of green hydrogen by providing a reliable source of low-cost distilled water.